45
minutes to reach the platform by helicopter.
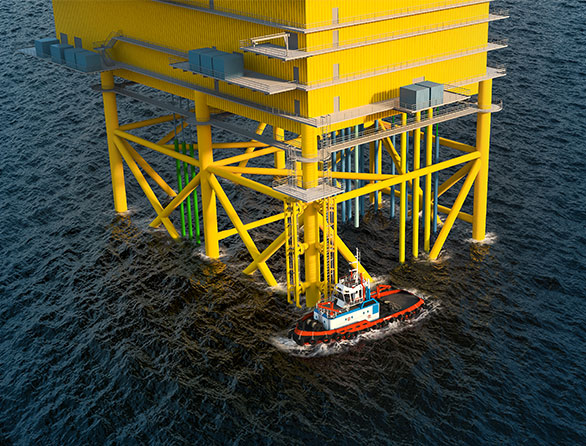
The converter platforms are located 60 and 125 kilometres from the mainland. Each transport run must be planned meticulously.
FAR OUT AT SEA
The location on the high seas presents a genuine logistical challenge for the planners. This is because the platforms are manufactured onshore and only then shipped to their installation location. The smaller and lighter they are, the easier they are to transport. “Every cubic metre of extra space not only adds weight, it adds cost,” explains Wegener. Individual components must not exceed a certain size and weight, otherwise ships and cranes will not be able to transport them. “If we forget to pack a certain tool and it's missing during erection of the platform, that's a real problem,” says the Overall Project Manager Engineering, because it has to be brought in by helicopter or – if weather conditions are too poor to fly – by ship. “That's why we have to plan installation meticulously.” To avoid long turnaround times, the fitters stay in rooms provided on accommodation platforms – known as “jack-up barges” – out on the North Sea.
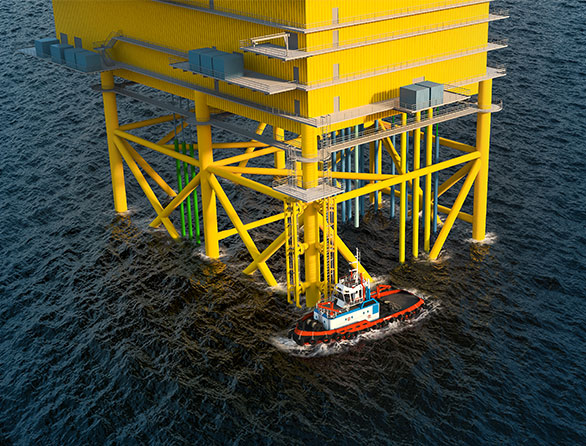
The converter platforms are located 60 and 125 kilometres from the mainland. Each transport run must be planned meticulously.